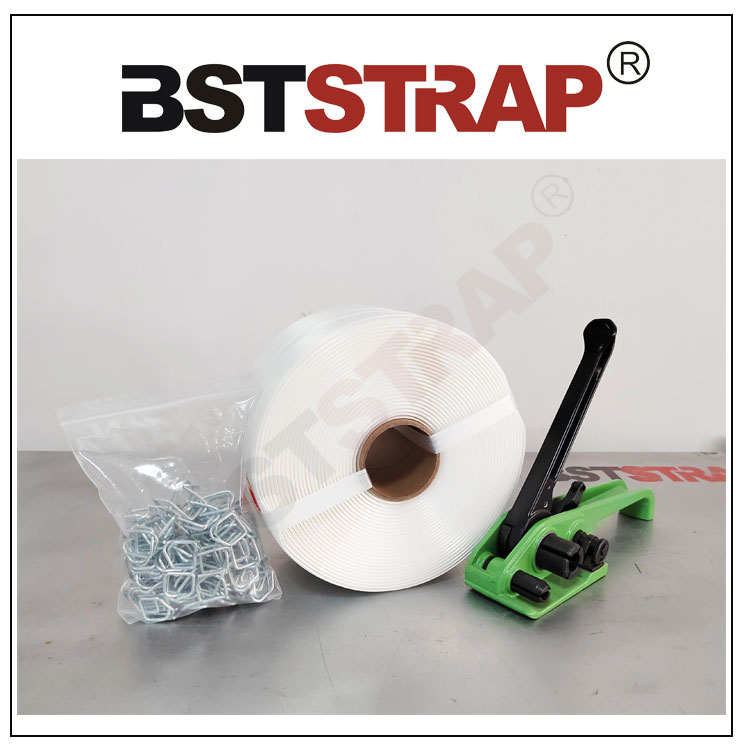
How Composite Corded Strapping is Made
Composite corded strapping has emerged as a leading solution in the packaging industry, known for its balance of strength, durability, and lightweight design. But how exactly is this innovative product made?
## 1. Material Selection
The initial step in producing composite corded strapping involves selecting the right materials. The core of composite strapping is typically made from a blend of high-tenacity polyester or polypropylene fibers. These materials are chosen for their strength and resistance to environmental factors, ensuring that the finished product can withstand heavy loads and adverse conditions.
Additionally, additives may be included to enhance properties such as UV resistance, moisture repellency, and overall durability. The right combination of these materials is crucial for the performance characteristics of the final strapping.
## 2. Fiber Processing
Once the materials have been selected, the next step is to process the fibers. The fibers are drawn and aligned to create a uniform structure. This alignment is critical, as it maximizes the tensile strength of the strapping.
After alignment, the fibers undergo a process known as texturing. This process twists and loops the fibers to increase their volume and resilience. Textured fibers provide better grip and holding power when used in strapping applications, contributing to overall performance.
## 3. Weaving the Strapping
With the processed fibers ready, the next phase is weaving them into a cohesive strap form. Specialized machines are used to weave the fibers into a flat, robust strap. This weaving process is essential for achieving the desired width, thickness, and density of the strapping, tailoring it to meet specific application requirements.
Throughout the weaving process, manufacturers monitor the tension and alignment of the fibers to ensure a consistent product. Any discrepancies are corrected in real time to maintain quality standards.
## 4. Coating and Finishing
After weaving, the composite corded strapping typically undergoes a coating process. This involves applying a protective layer that enhances the strapping's resistance to environmental factors such as moisture, UV rays, and chemicals. The coating can also improve the strapping's surface properties, making it easier to handle and reducing friction during application.
Once coated, the strapping may go through additional finishing processes, such as cutting to desired lengths or treating the edges to prevent fraying. Quality control checks are performed at every stage to ensure that the final product meets stringent standards for strength and reliability.
## 5. Quality Control
Quality assurance is a vital component of the manufacturing process. Throughout production, samples of the corded strapping are tested for tensile strength, elongation, and resistance to various environmental conditions. These tests help ensure that the strapping meets industry regulations and customer specifications.
After passing all quality checks, the strapping is rolled and packaged for shipping. Manufacturers often provide specifications, such as load capacity and recommended applications, to help customers make informed choices about the strapping they use.
## Conclusion
The manufacturing of composite corded strapping is a complex and meticulous process that combines advanced material science, engineering precision, and stringent quality control. From selecting high-quality fibers to weaving and finishing, every step is designed to create a product that meets the demanding needs of the packaging industry.